Save Huge Cost: Working with Speaker Enclosure Injection Molding Factory
- Share
- publisher
- AUSMAN AUDIO
- Issue Time
- Jan 5,2024
Summary
In this article, as one of China's leading speaker manufacturers, we'll dive into the intricacies of speaker enclosure plastic injection molding and how it can revolutionize the manufacturing process and your expense.

Cost Comparison of Different Plastic Speaker Molds
The Mold Cost of Different Types of Speaker Plastic Cases
First, we list 3 common speaker enclosure mold costs based on our manufacturing experience.
Molding Cost of Plastic Speaker Enclosure In AUSMAN
Speaker Type
|
Box Material
|
Molding Cost
|
Time |
Monthly Output
|
Soundbar Speaker
|
PP
|
$500-1000
|
15-30 Days |
50,000 Units
|
Party Speaker
|
PP
|
$5000-10000
|
30-90 Days |
20,000 Units
|
Plastic-wood Speaker | ABS+Wood | $40000-60000 | 30-90 Days | 5000-10000 Units |
Remark:
1. The Mold cost This is the industry average data. And of course there are molding cost for diferent supplier.
2. The output is calculated based on the scale of AUSMAN's injection molding factory and assembly factory.
Our injection molding factory has a total of 16 injection molding machines and two assembly bases with a total of 12 assembly lines.
Why Suppliers with Mold Workshop Can Save Huge Cost ?
Take Speaker Manufacturer AUSMAN For Example
Currently, we have more than 500 mass-produced models of plastic speakers, and these basic models provide you with a huge choice.
You can customize our base model to your local market needs. So you only pay a lower cost and get a brand-differentiated product.
In addition, even if you develop a new mold, you can sign a long-term cooperation plan with AUSMAN and we will return the mold cost to you in stages. It means that you can a free mold by working with AUSMAN ADUIO China.
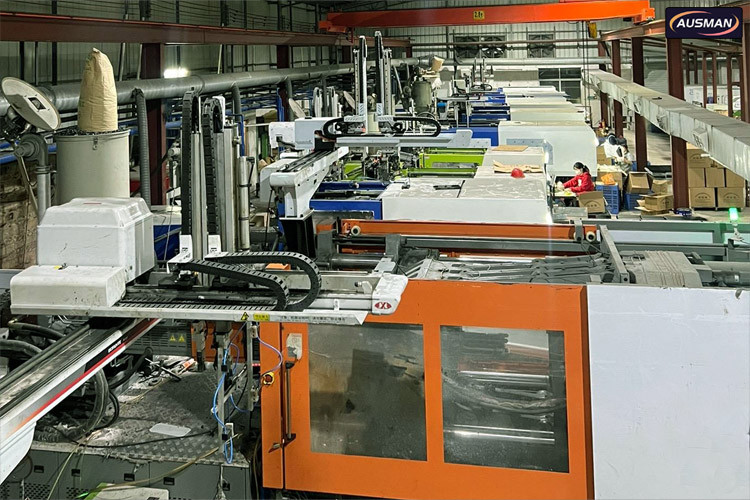
Speaker Enclosures Plastic Injection Molding
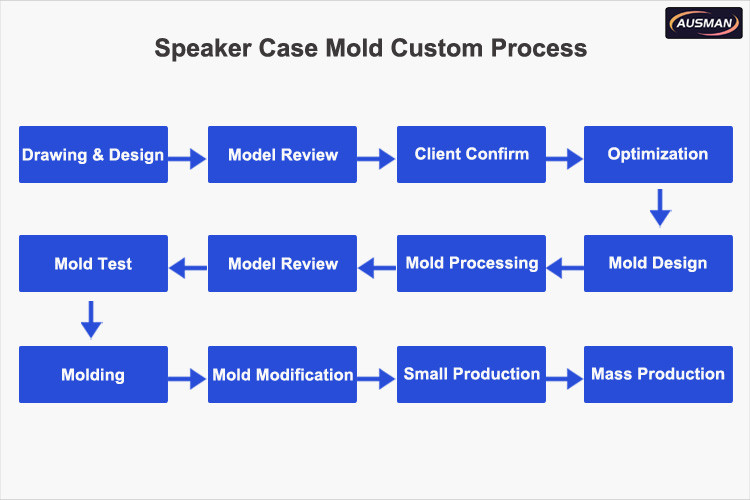
The Huge Advantage of Speaker Suppliers With Mold Workshops
In this article, as one of China's leading speaker manufacturers, we'll dive into the intricacies of speaker enclosure plastic injection molding and how it can revolutionize the manufacturing process and your expense.
If you are in need of development a new plastic speaker model, leave a message, we will feedback with a custome OEM/ODM solution
30-Ton Injection Molding Machine In AUSMAN
Plastic Speaker Enclosure Injection Molding Process
This is a 30-Ton Injection Molding Machine, and now it is manufacturing the back case of the portable party speakers. It can provide 200-300 front or back cases a day.
About Speaker Enclosures Manufacturing
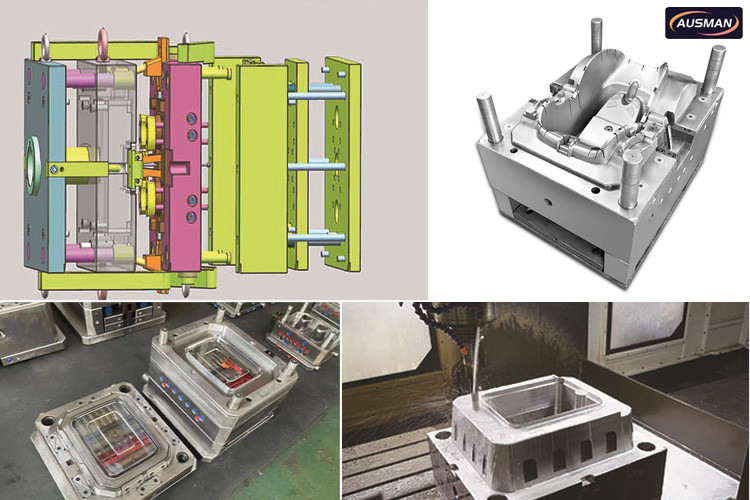
Plastic Boxes Are Better Than Traditional Boxes?
In speaker manufacturing, the speaker box is one of the three most important components: speaker box, drive unit, and power amplifier board.
Boxes made of materials such as wood or metal have high raw material prices and low production efficiency, resulting in high final production costs.
Therefore, manufacturers have been looking for alternatives to both.
Plastic injection molding shell design is flexible, and production efficiency, also reduce the cost.
Benefits of Plastic Speaker Enclosures
Plastic Speaker Enclosures Bring A Trifecta of Benefits.
1.They significantly reduce weight, enhancing portability without compromising structural integrity.
2.Their durability makes them resilient against environmental factors, ensuring longevity.
3.The customizability of plastic allows for unique and intricate designs, providing a personalized touch to audio systems.
4.Plastic speaker casings are suitable for large-scale mold production, and the output is high, effectively reducing the unit price of the product.
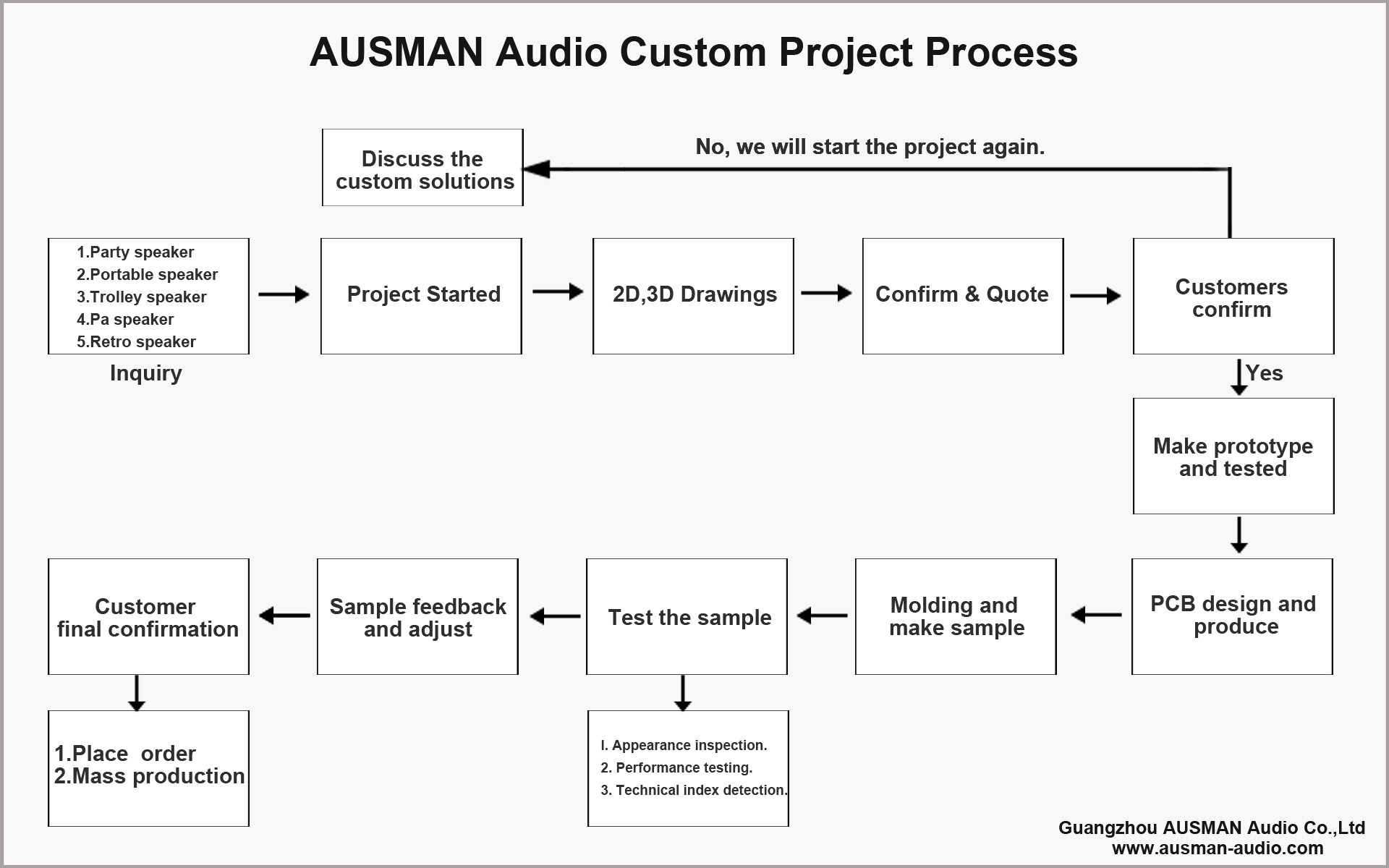
Speaker Plastic Case Injection Molding
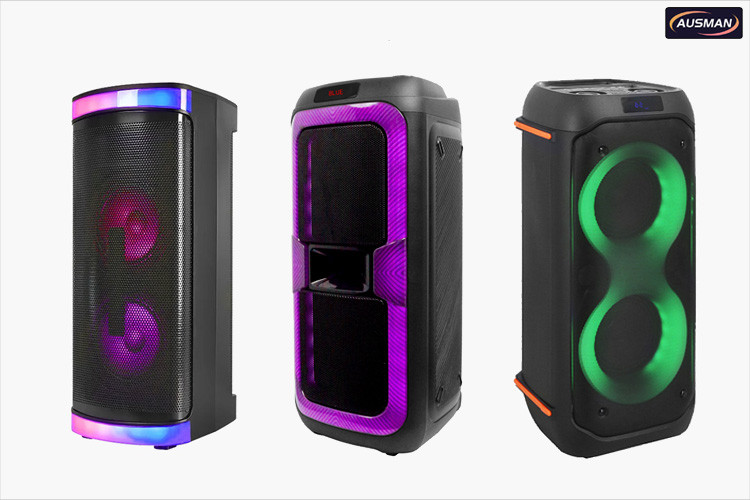
Efficiency and Precision
Central to the cost-effectiveness of plastic speaker enclosures is the process of plastic injection molding.
This manufacturing technique involves injecting molten plastic into a mold, creating precise and uniform shapes.
The efficiency and precision of this method make it an ideal choice for producing speaker enclosures.
Custom Plastic Speaker Enclosures
Highly Flexible Modeling Design
One of the standout features of plastic speaker enclosures is the ability to customize designs according to specific requirements.
Manufacturers can tailor the enclosure to meet precise specifications, providing a unique product that aligns perfectly with the desired audio experience.
This level of customization ensures that you get exactly what you need without unnecessary expenses.
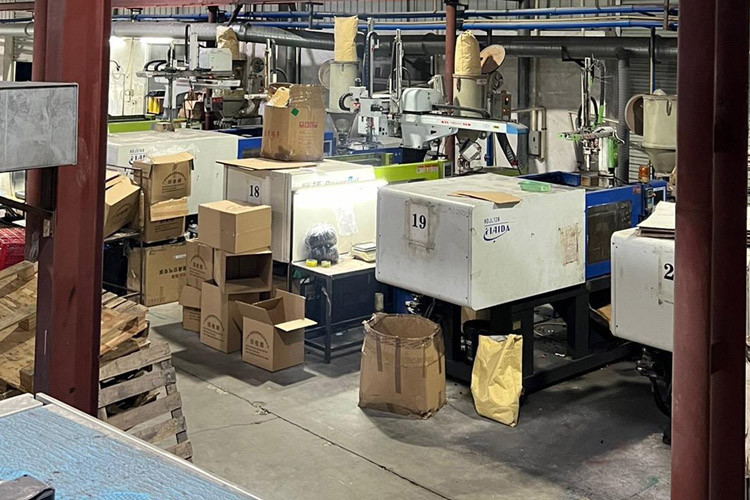
Finding the Right Manufacturer
Speaker Suppliers with Mold Workshops Brings You Economic Benefits
To harness the full potential of plastic injection molding, choosing the right manufacturer is paramount. Reputable manufacturers with a track record of quality and reliability will not only ensure a smooth production process but also contribute to long-term cost savings through reduced defects and reworks.
Speaker Plastic Injection Molding Cost Factors
Speaker Suppliers with Mold Workshops Brings You Economic Benefits
As speaker wholesalers or buyers, you need to understand the complexity of the cost factors in the process of plastic injection molding, which is vital to optimize expenses. From material selection to mold design and production, each element will help the overall cost. For example, the molds of PP and ABS materials are huge. Through strategic management of these factors, cost saving can be achieved without damage to the quality of the final product.
Future Trends in Speaker Enclosure Manufacturing
Make Clear Development Trend Helps To Grasp The Product Design Direction
Looking ahead, advancements in plastic injection molding technology are poised to further enhance cost-saving possibilities. From faster production cycles to the integration of smart manufacturing techniques, the future holds exciting prospects for manufacturers and consumers alike.
Environmental Considerations
Plastics Are Renewable Data More In Line with Environmental Protection Policies
While focusing on cost savings, it's essential to acknowledge the environmental impact. Plastic injection molding, when approached responsibly, can align with sustainable practices. Choosing recyclable materials and implementing eco-friendly processes contribute to a greener manufacturing ecosystem.
Choosing the Right Plastic Material
Select The Right Material According To Product Positioning Requirements
Not all plastics are created equal, and the choice of material can influence both the performance and cost of speaker enclosures. Understanding the specific characteristics of different plastics empowers manufacturers to make informed decisions that strike the right balance between cost-effectiveness and functionality.
Suggestions On Custom Molding
Choosing a supplier with a speaker shell injection molding factory can save you huge mold fees.
This type of supplier has experience in design, development, mold making and manufacturing, which not only provides you with choice when selecting styles, but also can redesign and customize products based on your brand needs.
Therefore, working with such suppliers is a huge advantage.
FAQs
Is Plastic Injection Molding Suitable For All Types of Speaker Enclosures?
Plastic injection molding is particularly suitable for various types of speaker enclosures, including those for home audio systems, car audio, and portable speakers. Its versatility allows for the creation of complex shapes and designs, catering to diverse audio requirements.
How Does Plastic Injection Molding Contribute To Weight Reduction In Speaker Enclosures?
Plastic materials used in injection molding are inherently lighter than traditional materials like wood or metal. This weight reduction enhances the portability of speaker enclosures without compromising structural integrity.
What Factors Should Be Considered When Choosing A Plastic For Speaker Enclosure Molding?
Factors such as the intended use, desired durability, and acoustic properties should be considered. Each type of plastic has unique characteristics, and selecting the right one ensures optimal performance and cost-effectiveness.
Are There Any Downsides To Using Plastic Injection Molding For Speaker Enclosures?
While plastic injection molding offers numerous advantages, it's essential to consider the environmental impact of plastic. Responsible material selection and disposal practices can mitigate these concerns.
l l Related Reference Resources